Refrigeración con baja carga de amoniaco (R717)
INTARCON2022-11-11T09:54:25+01:00Introducción
El progreso tecnológico en refrigeración en los últimos años se ha centrado en un número de estrategias bien conocidas, como son la eficiencia energética, el uso de refrigerantes naturales, en este caso con baja carga de amoniaco (R717), y la integración o prefabricación de los sistemas.
Además de la lucha contra el cambio climático, hay otro importante “driver” en el que se enmarcan estas estrategias y del que recientemente estamos siendo más conscientes que nunca, y es la escasez de recursos naturales: energéticos y materiales. Por esto en los años venideros es tan importante apostar por estas estrategias: eficiencia energética, refrigerantes naturales y optimización de los sistemas.
Una de las consecuencias naturales de estas estrategias es la reducción de carga de refrigerante de los sistemas, ya sea por una reducción del efecto invernadero de los refrigerantes fluorados, o bien por criterios de seguridad de los refrigerantes naturales, inflamables o tóxicos como es el caso del R290 y el amoniaco respectivamente.
En Intarcon hemos visto como desde que empezamos nuestra actividad hace 15 años, la carga de los sistemas se ha ido reduciendo en cada nuevo desarrollo: desde los sistemas inundados de amoniaco bombeado hasta los más innovadores chillers de carga crítica de amoniaco, pasando por gran número de sistemas cada vez más compactos. La reducción de carga entre los dos extremos es de más de 50 veces para la misma potencia frigorífica, o lo que es lo mismo, a menos del 2% de la carga original.
Baja carga de amoníaco (R717)
La pregunta es, ¿esto es baja carga de amoniaco?
Un criterio puede ser el criterio normativo. En estados unidos, a raíz de ciertos accidentes en instalaciones de amoniaco, se establecieron umbrales de Seguridad y Salud y de riesgo medioambiental en función del contenido de amoniaco de la instalación, como por ejemplo el límite de 500 lbs (225 kg) a partir del cual se precisa registrar la instalación de riesgo ante la EPA. En Europa no hay una normativa similar común en este respecto, pero algunos países como Francia sí tienen una política similar (por ejemplo a partir de 150kg se precisa la declaración de riesgo medioambiental). Otras normas de seguridad como la EN 378, de diseño de sistemas frigoríficos, sí establecen requisitos de seguridad en función de la carga de cada circuito. Por otra parte, el reglamento europeo de transporte por carretera (ADR) que requiere un transporte especial a partir de 50kg de amoniaco
Es decir, desde el punto de vista normativo no hay un criterio claro sobre lo que sería baja carga, aunque por ejemplo aquí en Europa, menos de 50 kg de amoniaco tiene grandes ventajas. Se pueden hacer sistemas precargados que se transportan por carretera y los requisitos de seguridad en el diseño son menores.
Desde otro punto de vista, si analizamos la literatura técnica veremos que el concepto de baja carga difiere entre distintos autores y entre distintas corrientes tecnológicas de uno u otro país. En estados Unidos llaman baja carga a los sistemas inundados de amoniaco con baja tasa de recirculación, que vienen a tener una carga específica en torno a 1,5 kg/kW, mientras que en Australia denominan baja carga a los sistemas centralizados de expansión directa de amoniaco, en torno a 1 kg/kW. En Europa habitualmente nos referimos a los sistemas indirectos, con carga específica incluso inferior a los 100 g/kW, o bien a sistemas de expansión directa distribuidos con una carga específica del orden de 0.3 kg/kW.
Tecnología de baja carga de amoniaco (R717)
Empecemos pues comentando este último sistema, de expansión directa distribuida. En contraposición a la expansión directa centralizada, en que una central de compresores da servicio a múltiples servicios, en el sistema distribuido tendríamos varias centrales compactas dando servicio a uno o unos pocos servicios.
Este concepto de instalación distribuida no solo me permite fraccionar la carga de refrigerante, sino que el propio diseño de la central permite también reducir la carga. Esto es un ejemplo de la tecnología que hemos utilizado en las centrales Ammolite:
- Condensadores microcanal para condensación directa del amoniaco con aire seco. Es decir, sin efecto adiabático y sin consumo de agua.
- Compresores de tornillo semiherméticos con motor de imanes permanentes a velocidad variable, con economizador para baja temperatura.
- Evaporadores de tubo y aletas, de expansión directa, expansión seca, con válvula de expansión electrónica controlada por el sobrecalentamiento.
- Enfriamiento directo del aceite en un enfriador de aire.
- Recuperación de calor para producción de glicol caliente de desescarche.
- Aceite miscible.
Cabe destacar que este sistema necesita un recipiente de líquido de alta presión, aunque de reducido tamaño.
Análogamente en chillers de baja carga de amoniaco enfriados por aire encontramos idéntica tecnología, pero destacando algunas diferencias:
- El evaporador de placas de acero inoxidable
- El diseño en carga crítica, sin recipiente de líquido.
Aspectos clave en los sistemas de expansión directa
Los evaporadores de expansión directa, por ejemplo de tubos y aletas, requieren de un adecuado diseño para la distribución del refrigerante adaptado a los reducidos flujos másicos del amoniaco (en comparación con otros refrigerantes) con una mayor velocidad de paso para contrarrestar la mayor tendencia del amoniaco a la estratificación del flujo (debido a la gran diferencia de densidad entre líquido y vapor). Por este mismo motivo se suelen utilizar tubos con superficie de intercambio mejorada para favorecer el mojado completo del tubo. Estos a su vez son muy susceptibles de ensuciamiento por aceite (en caso de aceite no miscible).
Un evaporador de expansión directa de amoniaco equipado con válvula electrónica puede funcionar adecuadamente con un DT1 de 6 o 7K.
En un sistema de baja carga de amoniaco no es admisible ninguna fuga residual de refrigerante. Esto obliga a utilizar compresores semiherméticos, con motores de alta eficiencia refrigerados por gas.
Los sistemas de expansión directa necesitan también asegurar un subenfriamiento en las válvulas de expansión y evitar el flash-gas en las líneas de líquido, lo que se consigue mediante el economizador o subenfriador.
Por otra parte, está el contenido de agua en el amoniaco, que es muy perjudicial para el funcionamiento de los evaporadores de expansión directa. Cualquier presencia de agua en el sistema evita la evaporación completa del amoniaco en el evaporador, quedando una solución residual de amoniaco y agua al 20%. Hay varios sistemas para eliminar el agua, como por ejemplo por destilación, pero en nuestro caso utilizamos el propio aceite.
El aceite es un aspecto clave en el sistema Ammolite. A pesar de los sistemas de separación, el aceite migra inexorablemente hacia el evaporador y debe retornar hacia el compresor. Un aceite miscible a presiones y temperaturas de operación del evaporador se diluye en el líquido refrigerante a lo largo del evaporador, y retorna finalmente al compresor con un contenido de refrigerante de entre un 10% y 20% que reduce significativamente su viscosidad. Gracias a este buen retorno del aceite al compresor se simplifica el sistema de separación de aceite y se evitan los sistemas o labores de purga de aceite.
El enfriamiento directo del aceite respecto de los sistemas termosifón redunda en una mayor eficiencia, menor carga de refrigerante y simplicidad de control.
Finalmente la alta higroscopicidad del aceite PAG atrapando las moléculas de agua en su cadena polimérica garantiza un funcionamiento sin humedad en el circuito.
Construcción de la gama Ammolite
La integración de toda esta tecnología en una construcción compacta es lo que da lugar a la gama de producto Ammolite. Tanto las plantas enfriadoras como las centrales condensadas por aire destacan por su construcción modular de condensadores en V.
Los condensadores microcanal de condensación seca es un elemento clave en el concepto Ammolite. A menudo se argumenta que la condensación evaporativa permite una reducción del consumo energético, pero sin considerar el enorme consumo de agua que conlleva (aproximadamente 3 m3/h por kW frigorífico) ni el coste del agua tratada (unos 2 euros por m3).
El siguiente ejemplo corresponde a una planta enfriadora de 720kW que suministra glicol a -8ºC en una industria cárnica en Mataró (Barcelona). Posee dos circuitos independientes de refrigerante con una carga de amoniaco de 25kg por circuito.
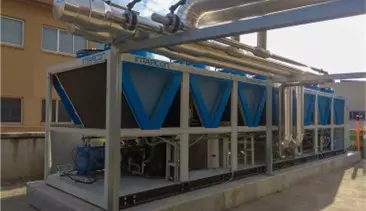
Ammolite también propone enfriadoras de glicol hasta temperaturas de salida de glicol de -30ºC. Aunque en bajas temperaturas los sistemas indirectos tienen ciertos inconvenientes, y es donde la expansión directa de amoniaco resulta más ventajosa. El siguiente ejemplo corresponde a dos centrales de expansión directa con sendos evaporadores de tubos y aletas que dan servicio a dos túneles de ultracongelación de carne. Están instalados en un matadero en Tarancón (Cuenca). Cada sistema tiene una carga total de 50kg de amoniaco para una potencia frigorífica de 120kW a -35ºC de evaporación.
Estos sistemas de expansión directa constituyen una novedad desde hace menos de un año. Una visión más detallada del túnel de ultracongelación se representa en el siguiente esquema. El conjunto se ha denominado “Turbofreezer” debido a las tres turbinas de alta presión que fuerzan el paso del aire a través de la carga. El evaporador de expansión directa, tiene un doble circuito de refrigerante y un circuito de desesescarche por glicol caliente producido mediante recuperación de calor del aceite.
Toda la instalación está monitorizada mediante el sistema kiconex con conexión a la nube, y que permite una visualización en tiempo real del funcionamiento.
El ciclo de congelación es un ciclo de unas 24 horas y tiene un coste energético de unos 0.1 kWh por kg de carne, aproximadamente un tercio del consumo de otros túneles de R448A que opera el mismo propietario.
Este Sistema de expansión directa de baja carga de amoniaco es aplicable a cámaras frigoríficas de baja temperatura, y con este objetivo desarrollamos junto con AEFYT el siguiente estudio del ciclo de vida del sistema de baja carga en comparación con otros refrigerantes (R449A y CO2).
El estudio muestra como a lo largo de un horizonte de 15 años el coste de vida del sistema de expansión directa de amoniaco arroja un menor coste de ciclo de vida gracias al menor coste energético de operación.
Conclusión
En conclusión, esta tecnología de baja carga de amoniaco se caracteriza por las siguientes ventajas y beneficios:
- Es una solución ecológica, sin efecto directo sobre el calentamiento global, y con mínimo impacto global gracias a su mayor eficiencia energética.
- Segura y fiable, debido a la reducida carga de amoniaco.
- Solución de fácil y rápida instalación gracias al concepto plug & play.
- Integra tecnología de industria 4.0 como el sistema kiconex de monitorización en la nube.
- Tiene un rápido retorno de la inversión relacionada con el sobrecoste respecto de tecnologías competitivas de menor coste inicial, gracias al óptimo coste de ciclo de vida.
Finalmente es importante tener presente la reflexión inicial sobre los retos a los que nos enfrentamos en las próximas décadas. No sólo estamos avocados a reducir nuestro impacto sobre el medio ambiente con sistemas eficientes de bajo consumo energético y de mínimo efecto invernadero. La nueva coyuntura mundial a la que nos enfrentamos nos llevará también a economizar los recursos naturales y materiales: reducir los consumos de agua y optimizar el uso de materiales a través de sistemas cada vez más compactos y optimizados.