Compressores de refrigeração industrial ou comercial
INTARCON2022-07-21T07:40:54+02:00Os compressores de refrigeração industrial ou comercial são a parte fundamental dos equipamentos e sistemas responsáveis pelo fornecimento e satisfação das necessidades de refrigeração de um espaço específico, câmara, processo…
Compressores: o núcleo dos sistemas de refrigeração
O que é um compressor de refrigeração?
O compressor é o principal componente do equipamento de refrigeração, a sua função é comprimir o gás ou fluido refrigerante, permitindo assim que ocorram alterações de pressão no gás ou fluido refrigerante, provocando o seu movimento ao longo do circuito do refrigerante.Estas alterações de pressão e temperatura ao longo do circuito do refrigerante levam a alterações no estado do gás ou fluido refrigerante à medida que este passa pelo condensador, válvula de expansão e evaporador. Com estas mudanças nas condições, o processo de refrigeração tem lugar num circuito básico de refrigeração. O compressor é assim responsável por que o refrigerante ou fluido refrigerante percorra todo o circuito de refrigeração, aumentando a pressão e a temperatura do refrigerante, fazendo com que os outros elementos mudem de estado.
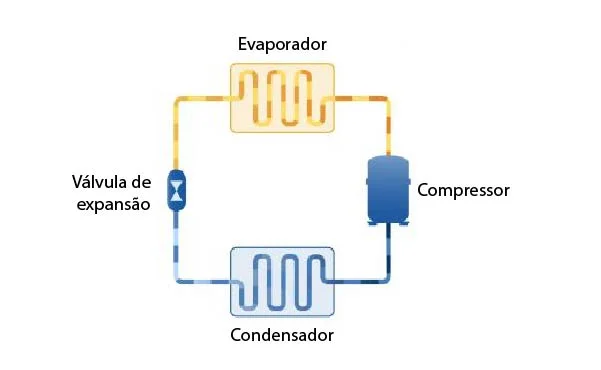
O funcionamento dos compressores é idêntico tanto em aplicações comerciais como industriais, a única diferença entre os dois poderia ser o tamanho dos compressores utilizados e os tipos de compressores, dependendo do equipamento de refrigeração seleccionado. Da mesma forma, a potência do compressor dependerá do campo de refrigeração, que pode ser comercial e industrial.
Qual é a função de um compressor de refrigeração industrial ou comercial?
- Este é o componente que transporta o gás refrigerante através do circuito do refrigerante.
- O compressor tem a função de comprimir o refrigerante que entra pelo lado de aspiração e de o empurrar para alta pressão e temperatura.
Tipos de compressores de refrigeração
Para uma correcta classificação dos tipos de compressores tanto para refrigeração industrial como comercial e o seu funcionamento básico, devemos ter em conta dois critérios principais que diferenciam o tipo de compressor: a sua tecnologia de compressão e a sua estrutura. Embora de uma forma geral a classificação dos tipos de compressores se baseie:
Compressores alternativos ou recíprocos.
O refrigerante é comprimido dentro de um cilindro graças ao movimento oscilante de um pistão por meio de uma cambota accionada por um motor eléctrico. Este tipo de compressor é caracterizado por:
- Têm válvulas de admissão e de escape que permitem um fluxo mais constante.
- A utilização de silent-blocks, a fim de mitigar as altas vibrações a que este tipo de compressor está sujeito.
- Visor de nível de óleo e resistência do cárter.
- Ligação para equilíbrio de óleo.
- Possibilidade de montagem individual, em tandem, trio ou rack.
Hermético. São utilizados em pequenas aplicações comerciais e caracterizam-se pelo facto de a sua estrutura estar coberta por um único invólucro contendo tanto o compressor como o motor de accionamento, o qual é totalmente selado, evitando assim possíveis fugas de refrigerante. No entanto, como resultado do contacto entre os componentes e o motor de accionamento, não podem ser utilizados refrigerantes como o amoníaco que possam danificar os materiais de que é composto. Têm também a desvantagem de não poderem ser reparados em caso de avaria.
- Semi-hermético. A sua aplicação é principalmente comercial e a sua construção tem duas caixas independentes para que tenhamos acesso à manutenção e reparação do compressor. Contudo, também há contacto entre o motor e o fluido refrigerante, pelo que determinados refrigerantes não podem ser utilizados e há um risco mais elevado de fuga.
- Aberto. A sua estrutura divide o motor e o compressor em dois módulos independentes, ligados por uma transmissão mecânica. Destacam-se pela sua total acessibilidade para reparação e manutenção, admitindo também qualquer fluido refrigerante e evitando o sobreaquecimento dos vapores antes da admissão no cilindro. Por outro lado, apresentam um maior risco de fugas.
Compressores rotativos.
Caracterizados por um fluxo de compressão contínua, uma vez que não dispõem de válvulas de sucção. Além disso, o óleo desempenha um papel importante neste tipo de compressor, uma vez que é responsável pela lubrificação e vedação. Vários tipos podem ser distinguidos de acordo com o tipo de movimento do rotor, embora os mais comuns sejam os mais comuns:
Palheta estacionária. O fluido refrigerante preenche o espaço entre o rotor do compressor e o estator, conduzindo o movimento do eixo do motor. O fluido é comprimido à medida que o seu espaço diminui no ponto de diâmetro mínimo dentro do compressor. Este tipo de compressor tem uma palheta localizada numa ranhura no cilindro, que é atribuída por uma mola. Esta mola é responsável por dividir a fase de sucção e a câmara de descarga do compressor.
- Scroll. O seu funcionamento é baseado no movimento orbital de uma espiral. É portanto formada por duas espirais idênticas, uma das quais é superior e fixa (estator), no centro da qual se encontra a porta de escape. medida que a espiral inferior (rotor) orbita dentro da espiral fixa (estator), o impulso das bolsas de fluido com as paredes faz com que se mova para dentro e subsequentemente aumenta a sua pressão.
- De parafuso. É utilizado para gamas de média e alta potência e a sua aplicação é industrial. É constituído por dois rotores de perfis conjugados, um dos quais, chamado “macho” e que está acoplado ao motor eléctrico, forma lóbulos, enquanto o outro “fêmea” tem alvéolos. A sua capacidade de regulação varia de 10 a 100%, graças a uma peça chamada lâmina, que abre ou fecha a abertura do fluido para os rotores para variar a potência. Estes compressores são lubrificados por injecção directa de óleo a uma temperatura controlada, fornecendo também selagem e absorvendo o calor da compressão. Têm também um separador de óleo e controlo de injecção de óleo.
Eficiência energética – Compressores de refrigeração industrial.
Quando falamos do compressor, estamos a referir-nos ao núcleo principal de um sistema de refrigeração, razão pela qual é importante falar sobre a sua eficiência energética e as diferentes alternativas que existem.
O compressor parafuso é actualmente o tipo mais utilizado na refrigeração industrial, embora em tempos tenha sido o compressor alternativo ou de pistão. As razões para esta mudança são:
- É possível obter mais capacidade de refrigeração com um único compressor de parafuso do que com um compressor alternativo:
- Embora o compressor parafuso tenha um custo mais elevado, a partir de certas capacidades, precisaremos apenas de um compressor parafuso em vez de vários alternativos, onde o custo inicial e o custo de manutenção seriam mais elevados.
- Com o compressor de parafuso é possível operar num único estágio a partir de temperaturas de evaporação mais baixas, apresentando assim uma maior taxa de compressão.
- É possível aproximar o funcionamento em duplo estágio com um único compressor de parafuso.
- A manutenção do compressor de parafuso é inferior.
- Os compressores de parafuso têm menos vibrações devido ao facto de não serem desequilibrados, ao contrário dos compressores alternativos.
No entanto, o compressor alternativo é mais uma vez uma alternativa viável no sector da refrigeração industrial, uma vez que é mais eficiente do que o compressor parafuso tanto em carga total como parcial.
Critérios de selecção dos compressores
Agora que estamos familiarizados com os aspectos gerais mais importantes dos compressores de refrigeração industrial e comercial, devemos tê-los em conta a fim de fazer a escolha certa:
- Capacidade de arrefecimento do sistema, dependendo das condições de funcionamento:
- Temperatura mínima de condensação: isto afectaria a lubrificação do compressor.
- Temperatura máxima de evaporação: afectaria um caudal de massa elevado, força excessiva sobre rolamentos, bielas…
- Temperatura máxima de condensação: isto afectaria a pressão máxima do compressor.
- Baixa temperatura de evaporação: afectaria o arrefecimento insuficiente do motor devido à baixa densidade do gás.
- Limite térmico: afectaria a temperatura de descarga demasiado alta.
- Dimensionamento do equipamento.
- Nível de ruído.