Direct and indirect cooling systems
INTARCON2023-07-21T07:55:44+02:00Refrigeration systems have more than one application, such as food preservation, equipment cooling, etc. It extracts heat from one environment and transfers it to another, thus cooling it first.
We have a wide variety of refrigeration systems, all of them different, which gives us the possibility to choose the cooling system that best suits our needs, what we are looking for.
In order to know which is the best in each situation, we must define them at various levels, and identify their advantages and disadvantages. In our article we will focus on learning more about direct and indirect refrigeration systems.
Direct and indirect refrigeration systems
Refrigeration systems can be classified as follows:
Direct systems: Compressed and condensed refrigerant gas leaves the machine rooms and is distributed to the remote user units (evaporators) (Figure 1a).
Indirect systems: The refrigerant gas is confined in the cooling generation zone, there the cooling power is transferred to an intermediate fluid, via an exchanger. The intermediate fluid, driven by a pumping system, transports it to end-users such as air coolers, exchangers, tank coils etc. (Figure 1b).
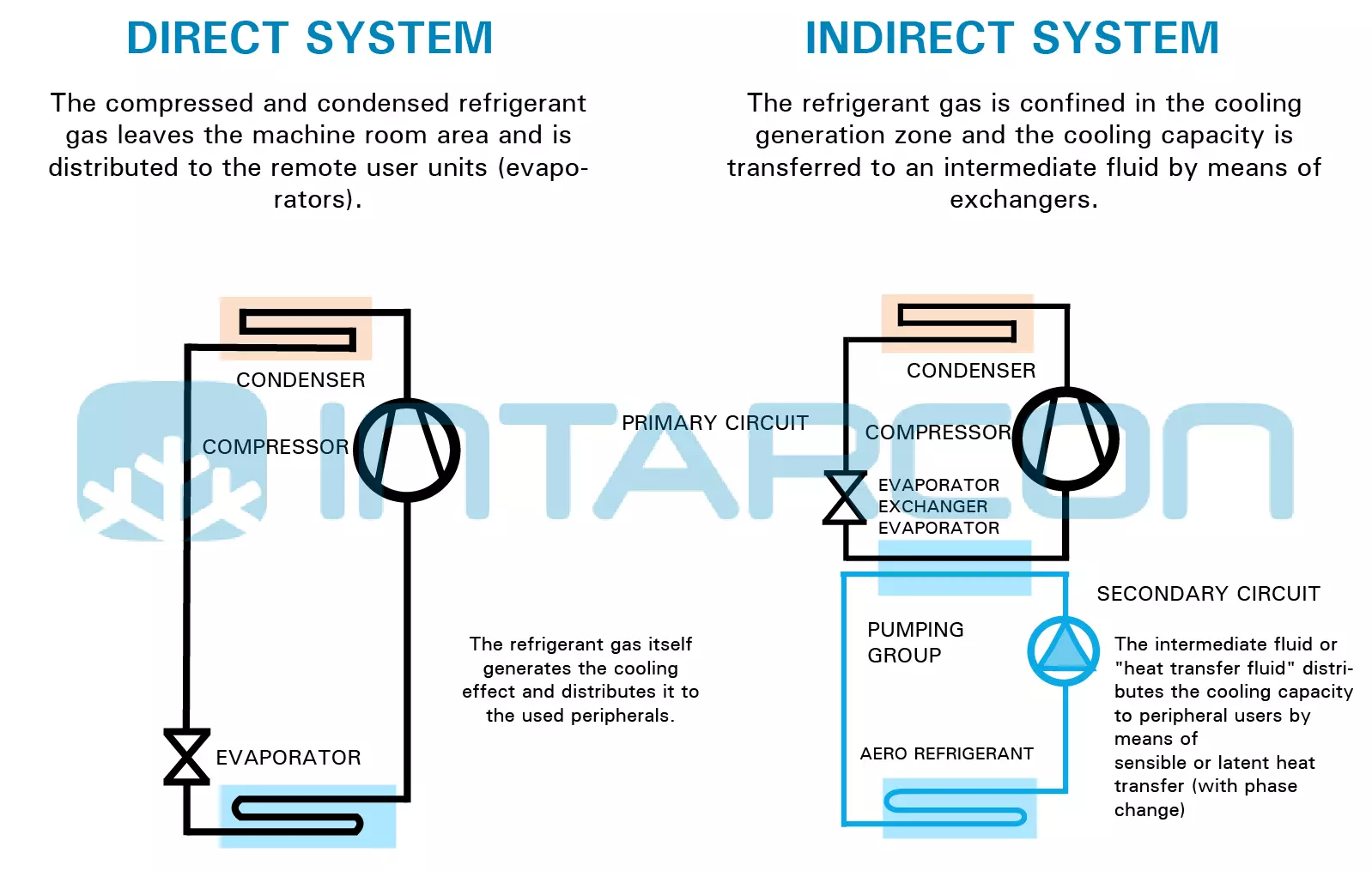
Indirect systems
Strengths and advantages
- Limits the risks associated with refrigerant leaks, reducing risks to people and the environment, minimising production losses.
- Reduction of the refrigerant charge compared to similar direct systems.
- It opens up the possibilities of using natural refrigerants such as R-717 and low GWP hydrocarbons and HFCs which, due to their toxicity and/or flammability, make them inadvisable for direct refrigeration installations, due to the high gas content and the extensive distribution network that reaches areas with the presence of personnel and products.
- Possibility of creating compact systems with the possibility of factory testing of operation and performance, resulting in “Plug & Play” products that do not require on-site refrigeration connections or long assembly and commissioning times. This type of system helps to guarantee not only contractual performance, but also to secure and shorten delivery times.
- To reduce pumping costs, especially when operating at low temperatures, it is possible to use alcohol-based fluids, ammonia water or phase change fluids. For example CO2 or “Ice Slurry” as a coolant or with peripheral CO2 cascade systems.
- It reduces the need for personnel with a high degree of specialisation in assembly, commissioning and maintenance to travel to the installations for long periods of time.
- It reduces the size of the engine room or simply eliminates it.
- Possibility of accumulation of cooling energy. Good examples are the dairy and brewing industry where cold storage tanks are commonly used.
Weaknesses and disadvantages
- Possible higher initial investment costs due to pumps and heat exchangers. On the other hand, there is a lower cost of the distribution system and air coolers, especially in the case of systems with R-717.
- These effects can be mitigated by the use of systems with variable flow rates of the intermediate fluid and the use of lower cost gases with better C.O.P., which are more difficult to use in direct systems.
Threats – BEWARE – The devil is in the detail!
- The secondary circuit IS NOT simple plumbing work.
- If a buffer tank is used, care must be taken in the design of the circuit to avoid mixing the return and discharge of the buffer fluid, especially with variable flow rates.
- With several chillers running in parallel take care of regulation in part-load system operation (ASHRAE Handbook – HVAC System and Equipment 11 – Carlo Pizzetti Refrigeration and Air Conditioning. Ch. 10.13)
- MEG, MPG and similar secondary fluids can be extremely corrosive in case of oxidation of their inhibitor and pH control components. Therefore, contact of the secondary fluid with the atmosphere should be avoided as much as possible during installation and maintenance operations. It is important to analyse the quality of the fluid during refilling and the correct selection of the expansion system.
- Careful selection of the materials for the secondary circuit and their design, according to the operating temperature, dilatations, supports and accurate choice of the best cost/quality ratio, e.g. welded stainless steel pipe UNE – EN10217-7 with low thickness – 76.1 x 2, 84 x 2, 104 x 2, 129 x 2. In plastic pipes, check compatibility with low temperatures and adapt the assembly system to the high dilatation indexe
- Correctly calculate the required thermal inertia, i.e. the necessary volume of secondary fluid, in relation to the cooling power, to ensure the correct operation of the chiller control system.
Opportunities for indirect cooling
- The current regulatory framework, where most HFC refrigerants tend to disappear or reach very high cost plus tax prices, opens a great market opportunity for the use of indirect refrigeration systems, where the refrigerant charge is much smaller and controlled.
- Similarly, if we focus on the Spanish regulations (RSIF’2019), installations consisting of indirect systems whose primary circuit is made up of compact equipment, whatever the refrigerant used, may be installed by level 1 installers. This opens a wide door to the marketing of this type of systems as they do not require such specialised installers.
Limitations of indirect systems
- For low-temperature applications, more complex and costly systems are required.
In order to choose one system over the other, it is advisable not only to assess the LCC (life cycle cost of the installation), but also to assess the risks to people, the environment and the customer’s business, such as production losses or contractual non-compliance in the delivery of products. Assess with the customer the impact of the refrigeration system on their production cost per unit of product. Finally, assess the possible lower cost of insurance premiums.